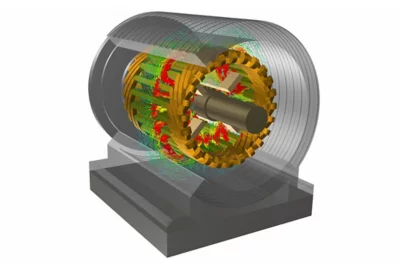
ANSYS ELECTRICAL MOTOR SIMULATION SOLUTIONS
The electric machine design industry has developed rapidly in recent years. Designs need to be developed in short timescales, integrated and designed as part of a wider complex system, and designed to be manufactured at scale. Engineers who design electric machines need simulation tools that can be employed for quick, accurate product development. Ansys’ electric machine design flow provides a complete virtual prototyping laboratory for machine design and development.
The Ansys electric machine simulation platform provides a complete solution for electric machine design and development. From the initial concept design stage to detailed multi-physics analysis and system validation, Ansys can provide a seamless end-to-end solution with couplings and automated workflows between various specialist tools.
The first piece in the workflow which covers the initial design of the machine with minimal input data to meet the target requirements is mostly done in Ansys Motor-CAD. Ansys Motor-CAD facilitates this cutting-edge design approach by providing the electric machine designer with a dedicated multi-physics design tool for electric motors. Motor-CAD provides rapid analysis over wide torque/speed operating ranges enabling comprehensive design space exploration. Within Motor-CAD there is a significant amount of embedded engineering expertise that can considerably expedite the design process. Motor-CAD is used worldwide in many different industries. It is particularly well adapted in the automotive and aerospace sectors where many class-leading manufacturers use it as a fundamental tool in their electric machine development process.
Ansys legacy workflow offers five combinable tools for designing and analyzing electrical machines. The new workflow replaces RMxprt with Motor-CAD which is a much more powerful tool and has a lot of multiphysics capability. This allows the designer to detect the issues early on in the design process. The new Ansys workflow which uses Motor-CAD instead of RMxper is as below and includes:
-
- RMxprt –for initial machine design
- Motor-CAD –for basic machine design which includes:
– Electromagnetic modeling capability
– Basic Thermal analysis
– Drive cycle performance modeling
– Initial Mechanical FEA analysis - Maxwell 2D/3D–for finite element analysis
- Simplorer–for system analysis
- Optimetrics–for Optimization/Design of Experiments
- Ansys Mechanical/CFD–for thermal, stress and acoustical analysis
Electric machine designs require appropriate electric drive circuits and the designed electric machine should work with the electric drive and digital control system. Ansys solution offers electrical machine co-simulation design with power electronics and control. Ansys Maxwell can be directly coupled with Ansys Simplorer and co-simulate during transient analyses. This capability enables engineers to analyze complex interactions between power electronics, control and magnetic component. Also, they can evaluate how nonlinear behavior of the motor affects the drive control loop performed in circuit simulator.
Electric machine design is a multi-physics problem. Multi-physics capability accelerates the design process, increases design accuracy, and can be used to optimize the performance of the electrical machine before the first physical prototype. Ansys Motor-CAD can provide multi-physics capability from the early stages of design which makes efficient multi-objective design optimization possible and provides a fast response to changing requirements. It includes electromagnetic, thermal, mechanical, and lab mode which can generate efficiency maps and performance across drive cycles.
The fully parameterized models from Motor-CAD may be exported to Maxwell 2D in seconds. The generated 2D o or 3D CAD generated in Motor -CAD may be saved and used in Ansys flagship solvers listed below :
- Ansys Maxwell for Electromagnetic Analysis
- Ansys Fluid for heat transfer coefficients
- Ansys Mechanical for Stress, Vibration & Thermal Analysis
Regarding optimization & robust design solution there is a need for efficient optimization techniques which can offer data-driven exploration of the design space while utilizing multi-physics simulation
- Electric machine design space is large with complex interactions.
- Use of Motor-CAD with optiSLang enables:
‐Class-leading multi-physics electric machine optimization.
‐Traceability on design decisions and data-based trade-off analysis.
‐Efficient multi-objective design optimization and fast response to changing requirements.
‐Robust design insights.
-Ration based geometry templates