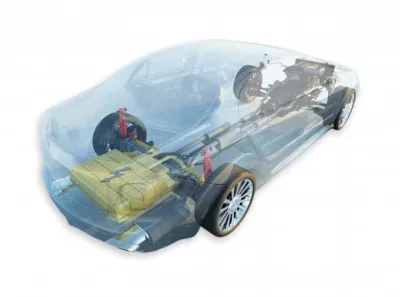
ANSYS BATTERY SIMULATION SOLUTIONS
Batteries are the key to every electronic device we now depend upon — especially smartphones and laptops — and they are the weak link in the system.
Batteries are the key driver in the world of portable devices. They are the critical component of our portable gadgets and are becoming increasingly important in our vehicles as well. The company that can engineer and get the most out of their batteries will clearly have a significant competitive advantage over the competition. Batteries, however, are clearly difficult to simulate due to their multiphysical, multiscale nature and how they are used in devices. Only Ansys, with its portfolio of industry leading software working together is up to the challenge.
Determine relevant performance characteristics of your potential battery cells with fully coupled electrochemical-thermal-flow models. Try out many different electrode designs in silico to get it right early on and avoid expensive prototyping and testing. Confidence in the design early on in the design cycle will allow you to get the most out of your product.
- Ensure temperature uniformity through fully coupled, multiphysics and multiscale models
- Heat generation
- Charge density
The Newman Electrochemisticty Model is used to perform the fully coupled, time dependent electrochemical-thermal-flow model of a battery cell in Ansys Fluent
Manufacturing defects, physical stress and unanticipated transient phenomena may all lead to unreliable or dangerous situations with a battery. Avoid and mitigate expensive failure modes and unacceptable safety issues.
- Create detailed mechanical models to simulate the battery under a variety of conditions.
- Gain insight into charge/discharge behaviour through coupled electro+thermal+circuit models
- Create detailed electrode and cell models to anticipate and deal with possible manufacturing defects
A promising new battery design is just the beginning for disruptive new technologies. Long term quality can be assured and designed for by a variety of in silico simulation techniques. Whether a warranty period is 2 or 20 years, company reputations for quality and technological leadership are made here.
- Simulate system behavior to account for complex interactions
- Model cyclic behavior to ensure long term performance and customer trust
- Specialized tools for battery modeling to enable comprehensive simulation
ROM and Digital Twins are very promising and favorable in our time and they have a lot of applications. Ansys platform allow us to create ROM and Digital Twin of batteries to predict the electro chemical and thermal behavior of batteries from cell to pack. Here are the steps to create ROM from Fluent results or test data:
- Create cell ECM from HPPC data
- Create module ECM using cell ECM
- Generate thermal ROM training data in Fluent
- Create LTI ROM in Twin Builder using training data generated by Fluent
- Couple the Module ECM and thermal LTI ROM in Twin Builder
- Create pack and connect to cooling pate if needed
ECM (Equivalent Circuit Model) represents the electro-chemical behavior using test data while Thermal ROM mimics the Thermal behavior. On the other hand, the ETC (Electro-Thermally Coupled) model include all these in one coupled model. The procedure is shown below:
Fig. 1) Steps of making a thermal ROM and ECM to create and ETC ROM in Ansys Twin Builder
Battery Management System (BMS) is crucial to battery pack safety and performance. BMS is batterie’s control center and keeps cells within specified operating range and shuts off battery when safety issues are detected. Software & hardware work in tandem to monitor battery performance and usage. BMS impacts weight, mechanical and thermal subsystems and requires compliance to Functional Safety Standards such as ISO 26262 (ASIL C, D). Ansys solution is to use Medini, SCADE and Twin Builder in tandem to develop the BMS in a very efficient way as the following:
- Using Ansys Medini for Safety analyses i.e. FTA, FEMA and HARA
- Ansys SCADE to connect safety requirements to generate a compliant code (Model Based)
- Using Twin Builder to do Physics-Based Battery Simulation
Fig. 1) Steps of developing and testing BMS using Medini, SCADE and finally Twin Builder
Fig. 2) A cost-effective solution for the development and verification of BMS
The benefits of using Ansys method can be listed as below:
- ANSYS Medini supports all Functional Safety Activities for ISO 26262
- ANSYS SCADE flow supports all software development activities for ISO 26262, ASPICE, AUTOSAR
- The gains of the approach are 40% to 50% of cost reduction demonstrated on user cases
- 2x Increase in time to market: Early detection of flaws, automated production of readable, portable, high performance and high-quality codes, and improved long-term maintainability