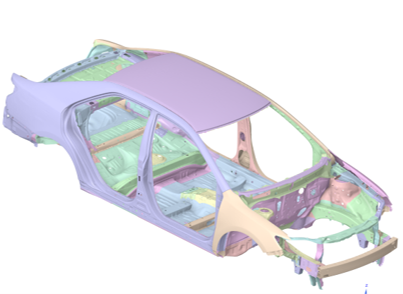
AUTOMOTIVE PAINTING PROCESS SIMULATION
Automotive paint shop is a critical part of car manufacturing, and this is not going to change with new wave of electric and autonomous vehicles. Painting is critical because it gives a feel for quality to customers and is critical for corrosion protection in the long run. There are new manufacturers and new factories with new models, all requiring paint planning. Modern car painting process involves multiple steps where careful preparation to achieve top quality is a must. First step is the e-coating where the body in white is dipped into an electrocoating solution, and a high voltage is applied for film build up. Follow-up is application of primer, base coat and clear coat layers via spray painting. Each of these steps include baking and cooling cycles in between. Uniform e-coat thickness is required for corrosion protection. There should not be any air entrapments or e-coat undrained during e-coating.
The baking process is required for curing of structural and cosmetic seals and proper heating is a must. Unequal or insufficient heating can result in different seal related quality problems. The uniform paint thickness at spray painting is critical as well. Too much or too less can cause orange peel or fish eye problems. All these problems can be predicted and planned in parallel with car design using Ansys tools. Multiphase fluid flow, electrostatics, particle tracking, wall film modeling, conjugate heat transfer and radiation, in other words the physics behind car paint shop can be modeled and tuned for perfection. Recent developments in Ansys tools also enables processing of complex and large automotive CAD geometries. Ozen Engineering has completed numerous consulting projects in regards to paint process modeling and can help companies paint shop planning. Ozen Engineering makes use of cloud computing as an enabler for large and long transient runs.
- First step of coating, negative charged vehicles is deposited with protective coating
- Ansys CFD provides tools to analyze coupled field analysis (electro-static and multiphase flow)
- Visualize the e-coat thickness on inner cavities, where the physical process requires teardown of the BIW
- Identify the reach of electric potential on inner cavities and take remedial actions early in the design cycle
- Test various BIW motion speeds to achieve minimum threshold and uniformity of paint thickness deposition
- During dipping air is displaced by e-coat liquid (VoF solution)
- Air entrapped inside causes bad coating
- CFD helps to predict these locations
- Enable designers to take precaution
- Design holes to let air escape
- Position, adjust active flow inside pool to push out
- Agitation cycle range of motion
- E-coat liquid is replaced by air during dip-out
- Any residual liquid can lead to quality issues and material waste
- Amount of liquid hold on vehicle can be monitored by time
- Drainage holes can be designed accordingly
- Orientation of the vehicle during drainage can be set accordingly
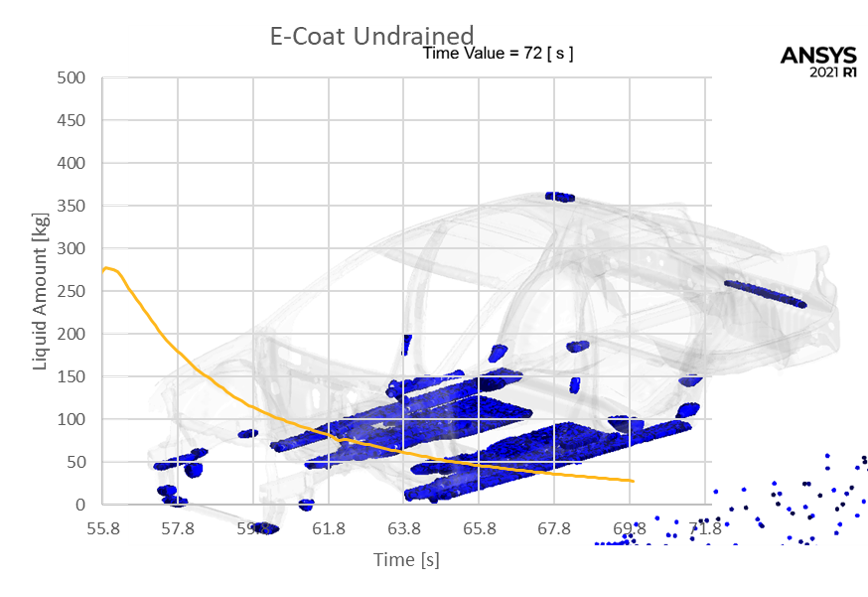
- BIW experiences higher hydrodynamics forces
- Large, thin sheet metal can buckle during travel inside liquid
- Ansys structural can predict buckling and possible plastic deformations
- Fluid Structure Interaction can be setup using pressure data from CFD solution
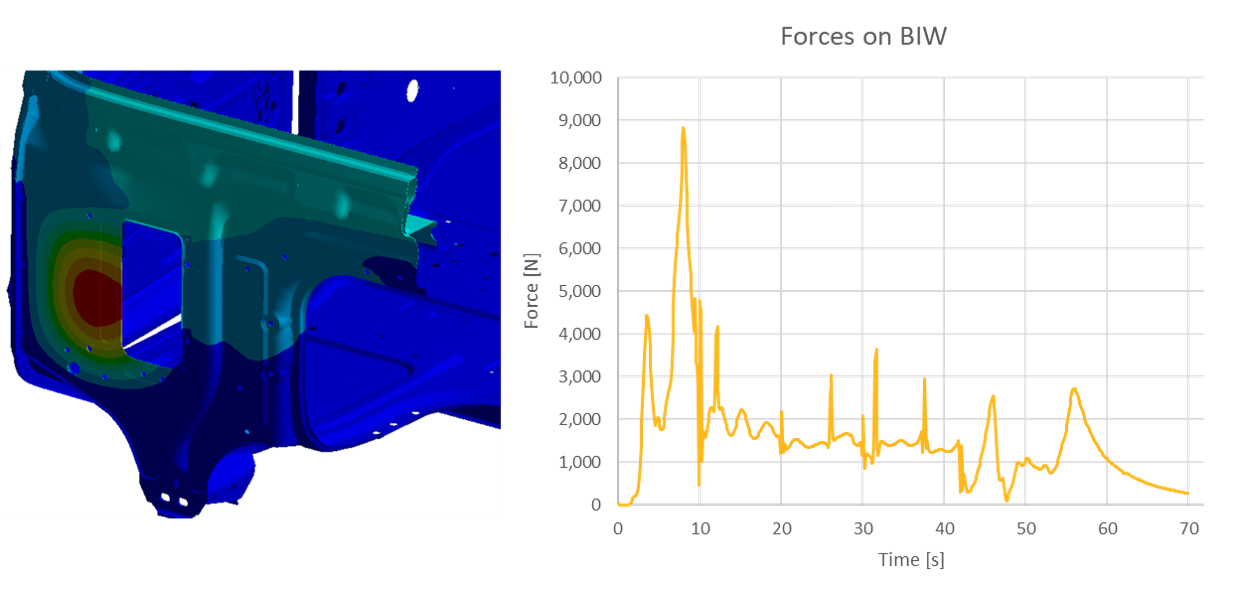
- The coated body-in-white parts are cross-linked and cured in the oven 185C-200C
- Required amount of heat needs to be applied at required amount of time
- Transient CFD is used to monitor temperature of BIW as a function of time
- Conjugate heat transfer with fluid and solid
- Moving/Sliding mesh solution
- Last two stages of the paint process involves spray painting
- Electrostatically charged paint particles are released from rotating cup bell shape
- Ansys CFD provides user defined functions to resolve interactions between electrostatic field and charged particles
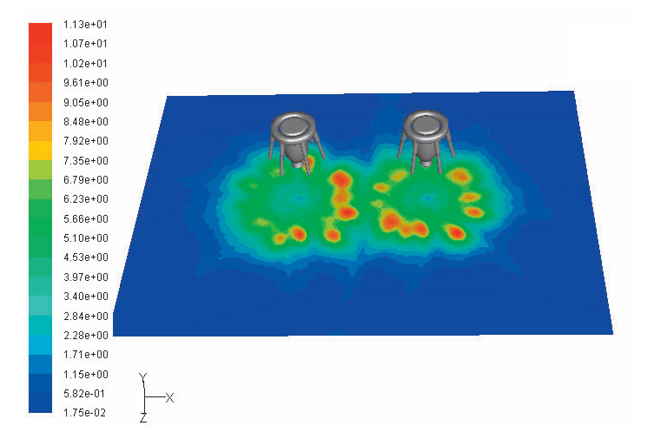
OZEN ENGINEERING AUTOMOTIVE PAINT PROCESS SIMULATIONS
Contact us to learn more or to schedule a demonstration.
Ecoat Dipping Process Animation
Electrocoating Pull Out Process
Oven Drying in Paint Process Simulation Help Understanding Temperature Time History