FEA Simulation Consulting
At Ozen Engineering, we offer advanced finite element analysis (FEA) simulation consulting, harnessing the power of Ansys Mechanical, Ansys LS-DYNA, Ansys Autodyn, and more. Our seasoned FEA consultants combine deep knowledge with practical expertise to optimize your structural analysis processes.
Our solutions include:
- In-depth Structural Analysis and Design
Leverage Ansys Mechanical, LS-DYNA, and Autodyn for detailed structural modeling, tackling stress distribution, dynamic impacts, and durability. - Expert-Level FEA Simulation Capabilities
Our specialists excel in refining simulation elements such as mesh detail, solver configurations, and material properties to deliver precise structural insights. - Enhanced Structural Optimization Techniques
Our streamlined FEA workflows enhance engineering efficiency, promoting robust design refinement, sensitivity testing, and superior performance.
Driving Innovation with FEA Expertise
At Ozen, we deploy top-tier Ansys FEA tools—Ansys Mechanical, Ansys LS-DYNA, Ansys Autodyn, Ansys Discovery, Ansys Sherlock and Ansys Motion—to provide targeted solutions across diverse sectors. Ansys Mechanical is essential for detailed simulations such as structural integrity tests, vibration analysis, and heat transfer, boosting efficiency in semiconductor, consumer products, automotive, and aerospace industries.
Ansys LS-DYNA is renowned for its ability to model complex nonlinear events such as impacts and explosions, whereas Ansys Autodyn offers specialized capabilities for blast applications. Ansys Discovery accelerates the early stages of design through fast and flexible modeling. Ansys Sherlock provides accurate electronics reliability predictions for hardware at the component, board and system levels. And Ansys Motion excels in simulating rigid body dynamics, providing precise analysis for mechanical systems.
If your projects demand precision and cutting-edge FEA solutions, contact us today. Let’s collaborate to turn your engineering challenges into competitive advantages.
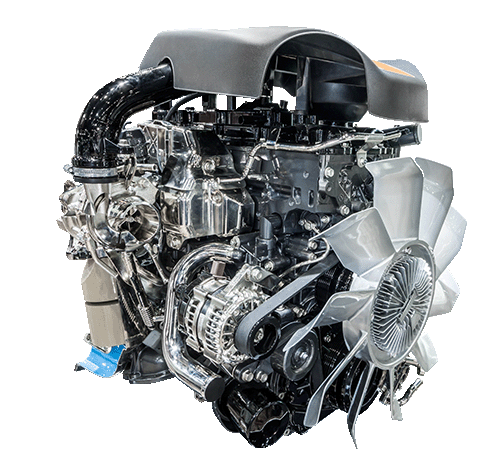
Structures Capabilities
Ansys Workbench
Ansys Workbench enables connections between analysis systems. For example, a prestressed modal analysis or fluid structure analysis.
Ansys Workbench
Strength Analysis
The strength of components sits as a key requirement in understanding a product’s performance, lifecycle and possible failure modes.
Strength Analysis
Vibration
Vibration can be an undesired side effect of poor product design or the environment in which the product is operating.
Vibration
Thermal Analysis
The effects of heat and thermal management on parts and assemblies is becoming increasingly critical as performance limits are pushed further by the need to have lighter, smaller and more efficient designs.
Thermal Analysis
Durability
Building durable products is key to reducing warranty costs and increasing reliability. Being able to understand how designs will behave over time as load cycles increase helps you avoid unexpected failures.
Durability
Impact
Impact between two or more bodies is modeled by the Ansys structural family of programs, including mechanical, explicit dynamics and rigid body dynamics.
Impact
Structural Optimization
Ansys optimization technology includes parametric, shape (mesh morphing) and topology optimization.
Structural Optimization
Rigid and Multi Body Dynamics
Mechanical devices can contain complex assemblies of interconnected parts undergoing large overall motions.
Rigid and Multi Body Dynamics
Hydrodynamics
Offshore structures are subjected to environmental loading from the effects of waves, currents and wind.
Hydrodynamics
Composites
The light, strong and versatile properties of composite materials make them attractive for many types of manufacturing.
Composites
Additive Manufacturing
Ansys Additive Solution delivers the critical insights required by designers, engineers and analysts for a successful Additive Manufacturing Process, to avoid build failures and create parts that accurately conform to design specifications.
Additive Manufacturing
Multiphysics
A vast range of multiphysics capabilities from simple thermal structural analysis to coupled field analyses using finite element analyses are available.